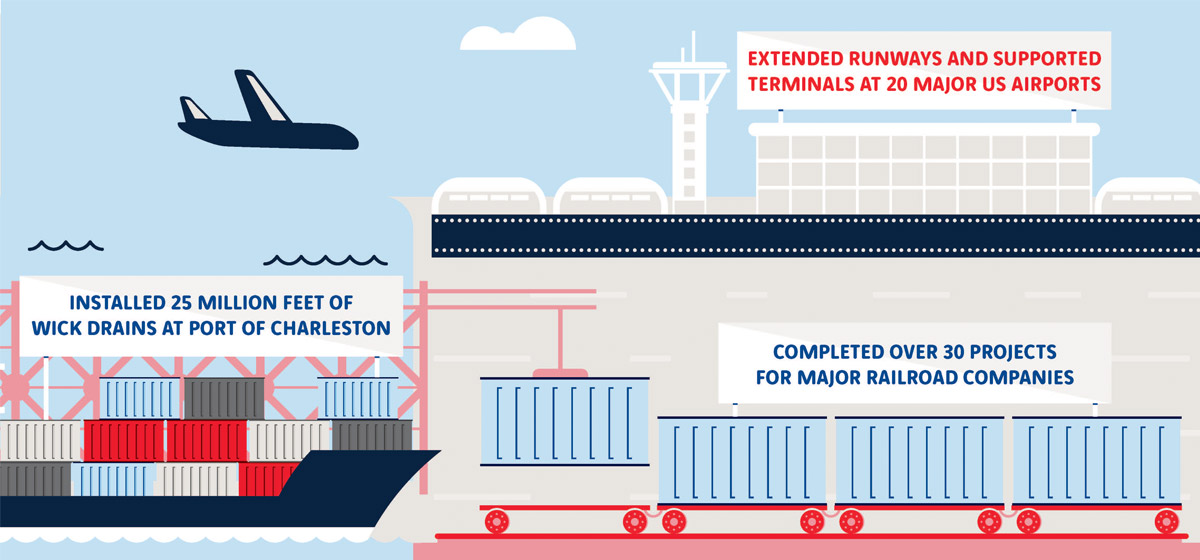
The pressure to fulfill orders within days or even hours is driving change and innovation for not just retailers, e-commerce vendors and warehouse developers, but also the shipping and packaging industries- and of course, the construction industry. Their collective goal is to fulfill orders while cutting cost and delivery times. Menard USA’s goal is to provide reliable ground support along the way.
The “Amazon Effect” has created a revolution for retailers and those involved in supply chain logistics. People want their stuff NOW, and they want it CHEAP! Almost 60% of all online transactions now include free shipping, requiring retailers to get closer to their customers to meet the NOW and CHEAP demand. The success of Amazon Prime’s free two-day shipping is creating a “new normal” for customer expectations, and the trend is having a significant impact on the logistics landscape that Menard USA helps support.
In 2006, Amazon had 8 city-centered fulfillment locations. By 2016, that number had reached 90 – and is now growing at an even faster pace. In order for other e-commerce retailers to remain competitive with Amazon, they also need to have warehouses and fulfillment centers in highly populated areas and be constantly innovating to improve their “last mile delivery”.
The ideal location for these warehouses and fulfillment centers has three major requirements, and Menard has helped them meet their ground improvement challenges:
- Proximity to a transportation hub, such as a major airport or port. On runways and docks, we’ve designed and installed Controlled Modulus Columns (CMC)® rigid inclusions , wick drains and earthquake drains to make sure they remain stable when they are typically in coastal areas, near rivers or on manmade fill.
- Easy access to major infrastructure like railways and highways. CMC rigid inclusions, dynamic compaction and wick drains are just a few of the solutions we’ve used to support embankments along rails and roads.
- Close to a highly and densely populated metropolitan area. We’ve worked along busy roadways, in narrow city streets and in confined spaces because our technology generates no vibration and has virtually no spoil- which can be a plus in contaminated soils often found in industrial areas near cities.
The New Jersey/New York corridor shows the evidence of this boom in warehouse space and infrastructure development in response to the “Amazon Effect”. Industrial vacancies have been driven to an all-time low, the Newark airport and port are rapidly expanding, and highway expansion and widening projects are improving access to these areas. Large markets like Los Angeles, Chicago, Atlanta and Houston are seeing similar growth, and even smaller markets like Charleston are having to expand to meet demand.
The boom has also had a domino effect on the economy in these areas, causing third party logistics suppliers like UPS and FedEx to multiply and see a significant increase in business. Smaller retailers are able to outsource their logistics and fulfillment to centers like these, which eliminates the need to have their own warehouses, decreases the delivery time to their customers and levels the playing field with larger competitors.
New technology and products to further improve the supply chain are on the horizon. Uber for Freight, self-driving cars, renewable energy, automated warehouses and drone deliveries are just a few of the innovations that could shake up the logistical landscape in the future.
Menard USA is excited to support each piece of the supply chain from stabilizing runways at major airports and railways along train routes, to strengthening the ground under highways and warehouses, and we welcome the challenges new innovation in logistics brings.