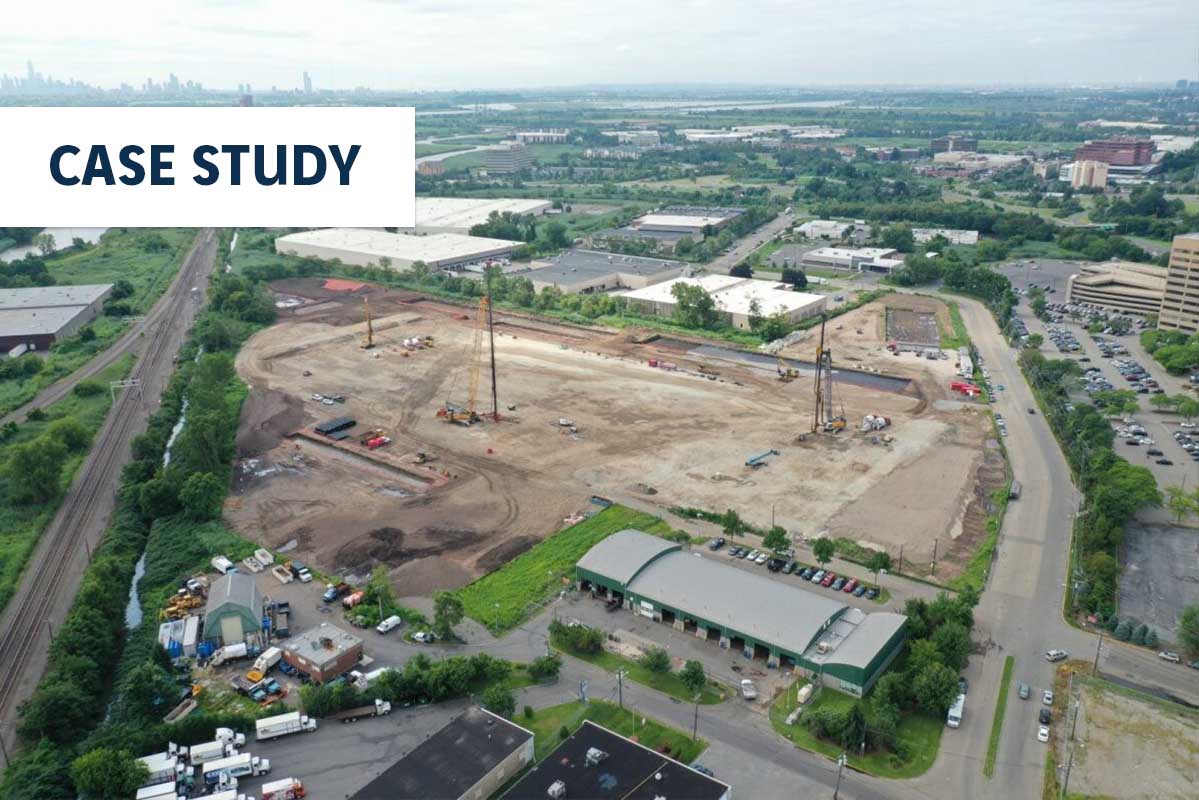
Highland Cross
Highland Cross
Project Details:
Owner: Lincoln Equities Group, LLC
General Contractor: R.C. Andersen, LLC
Date of Work: July 2021 - December 2021
Engineer: Langan Engineering
Approximate Key Quantities: Controlled Modulus Column® rigid inclusions - 5,859 EA.
Project Overview:
Northern New Jersey, an active market for warehouse development, added a 355,392 sq-ft facility on the 25- acre Highland Cross Industrial site in Rutherford, NJ. The new warehouse will serve as a “last-mile” delivery center for a major e-commerce company. It is located at the crossroads of the New Jersey Turnpike and Routes 3 and 17, offering convenient access to New York City, the Port of NY/NJ and 18 million consumers within a one-hour drive. The site is bound by a Department of Public Works facility to the north, Veterans Boulevard to the west, various one-story warehouses to the south, and Conrail railroad tracks to the east. In addition to the new warehouse, the project also features cross-docked loading, more than 70 dock-high doors and more than 80 trailer parking spaces. Due to the loose and compressible nature of the soils at the site, excessive settlement was predicted within the compressible fill and soft soil deposits underlying the site. Menard was contracted to provide ground improvement for the new warehouse – the selected technique was Controlled Modulus Column
(CMC)® rigid inclusions.
Ground Conditions:
Solution:
The geotechnical report recommended a variety of options to support the new structure, which included tapertube piles; pipe piles; auger cast-in-place piles, and rigid inclusions. CMC rigid inclusions were ultimately chosen as the most economical and timely method. Due to the anticipated installation depths, cranes and leads were required for CMC installation. Two crane and leads setups were used to install the elements to a termination depth up to 162 ft, while a Bauer drill rig installed shallower CMCs. In all, 5,859 CMCs were installed to an average depth of 96 ft and a maximum depth of 162.73 ft. Menard’s design accounted for building column loads ranging from 72 kips to 600 kips, exterior wall loads ranging from 4.6 kips to 5.7 kips per linear foot, and live load on the building slab of 800 psf. Menard’s design also included the support of up to 7 ft of fill in areas of the site. The fill was required to reach the bottom of slab elevation. Menard’s design provided for 2 ins of postconstruction settlement with ¾-in of differential settlement, meeting the performance criteria of the new facility.
The projected duration of CMC installation was five months. Various challenges such as utility re-location, extended CMC depths in various locations, and inclement weather increased the duration, but just slightly. All CMCs were successfully installed -- and done so in coordination with the footing and precast subcontractors -- to meet the overall project schedule. Menard USA successfully installed nearly 6,000 CMCs to support a 355,392 sq-ft warehouse in Rutherford, NJ.
Print this resource