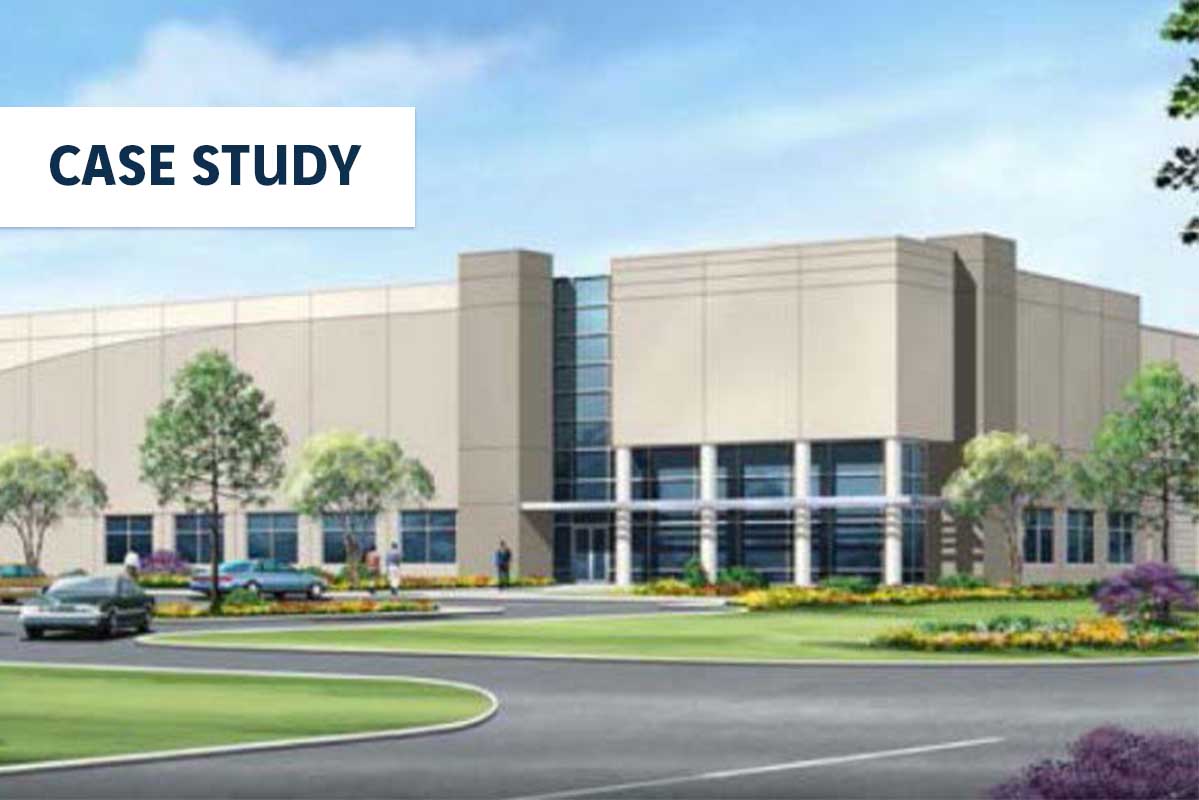
Medline St. Peter's
Medline St. Peter's
Project Details:
Owner: Medline
General Contractor: Alston Construction
Date of Work: May 2020 to August 2020
Engineer: SES, LLC
Approximate Key Quantities: CMCs - 10,795 EA.
Project Overview:
Medline, a Chicago-based manufacturer and distributor of medical supplies, proposed the construction of a one-story, 47-ft tall, 811,300 sq-ft office/warehouse building to be located in the Premier 370 Business Park in St. Peters, MO. As the world’s largest privately held manufacturer of medical supplies, Medline acquired 52 acres in the St. Peters location to serve the medical needs of residents in nearby St. Louis and the surrounding area.
In addition to the new building, Medline proposed the construction of two small generator pads outside of the building footprint.
Due to the compressible and loose nature of the soils at the site, Menard Group USA was contracted to support the future distribution center and generator pads – the selected technique was Controlled Modulus Column (CMC)® rigid inclusions.
Ground Conditions:
Solution:
Menard proposed CMC rigid inclusions to support the entire facility and to improve poor soils -- allowing for spread footings and slab-on-grade construction. Other rigid inclusion systems were considered; however, those systems accounted only for the warehouse storage areas and not the offices and equipment bays. Menard’s solution provided a more economical and schedule -saving ground improvement system.
Menard’s solution included 10,765 CMC rigid inclusions (totaling 466,546 LF) installed to an average depth of 43 ft and a maximum depth of 78 ft. The design provided for 1 in of post-construction settlement with less than a ½- in of differential settlement between footings, meeting the performance criteria of the new building. The slab loads were designed with an allowable bearing pressure of 375 psf with footings designed at 4,500 psf.
The site was not without its challenges. Inclement weather created a wet working platform and caused delays in schedule. The delivery of grout was also inconsistent. (The timely delivery of grout is essential for CMC installation). Moreover, a weeklong union strike and a weeklong shutdown due to a union hand contracting COVID-19 caused unexpected delays. Notwithstanding these challenges, Menard successfully provided CMC ground improvement and met the client’s requirements for quality, safety and schedule.
Print this resource