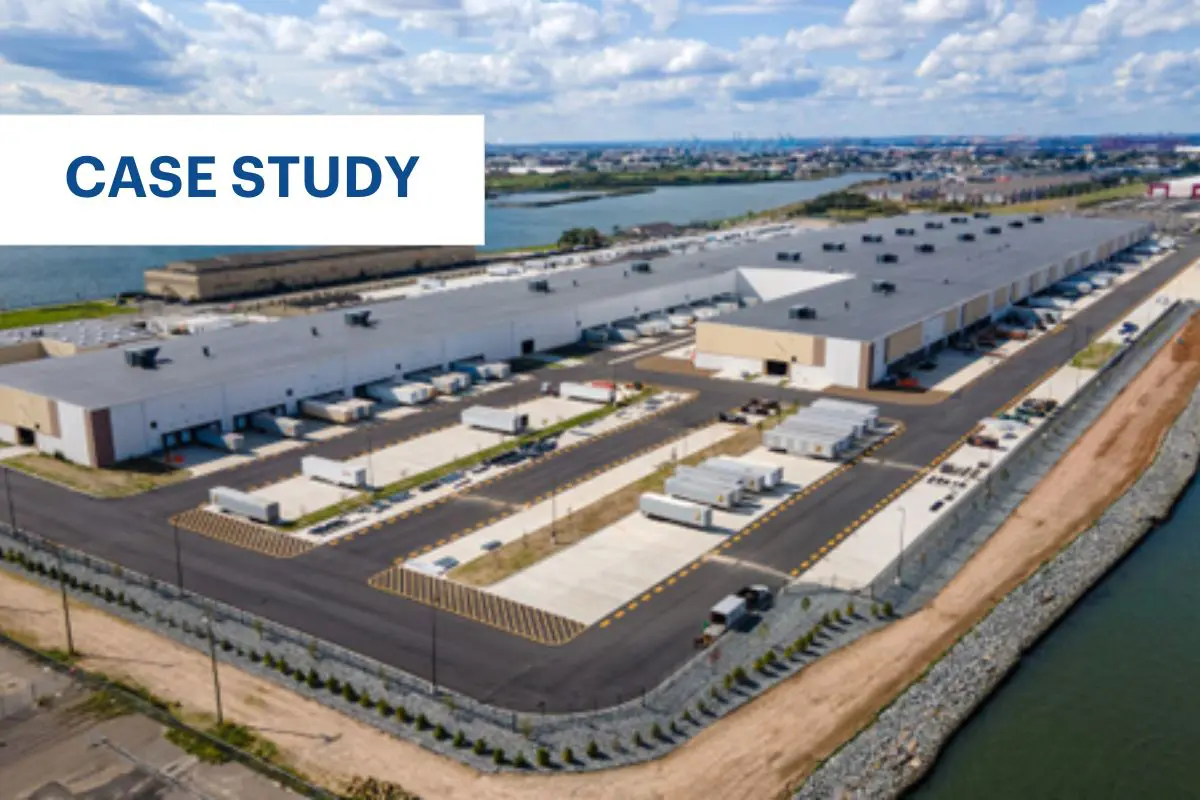
Bayonne Logistics Center
Bayonne Logistics Center
Project Details:
Owner: Lincoln Equities Group
General Contractor: Alston Construction Company, Inc.
Date of Work: August 2021 - May 2022
Engineer: Langan Engineering and Environmental Services (Civil); Smith, Roberts & Associations (Structural)
Approximate Key Quantities: Controlled Modulus Column (CMC)® rigid inclusions - 8,300 EA
Project Overview:
Ground Conditions:
Solution:
Menard proposed CMCs to limit settlement and provide the required bearing capacity for the strip and spread foundations, and slab-on-grade. Menard’s design evaluated the performance of 12.5-in diameter and 15.6-in diameter CMCs installed under isolated spread footings, wall footings, and slab-on-grade. The CMCs were installed through the fill and soft clay layer and terminated in the medium dense sand layer. The design provided for two in or less of total settlement for the footings. And a differential settlement between adjacent columns of ¾ in or less. The axial loads on the building columns vary from approximately 70 to 140 kips. Maximum wall loads are between 5.5 to 9.5 klf, and slab-on-grade load is from 500 to 1600 psf. The required allowable bearing capacity of the foundations is 4 ksf beneath the footings.
The slab area with 500 psf load between column lines 21 and 40 had been previously surcharged to at least elevation +20 ft. In this area, the post construction settlement without any ground improvement is fewer than 2 ins. Further, the resulting settlement without ground improvement falls more in line with the predicted settlement of the remaining areas of the building receiving ground improvement. To provide optimal support for the building -- and to further mitigate the potential for differential settlements between heavily surcharged areas of the site -- Menard recommended that ground improvement was not required for the slab-on-grade between column lines 21 and 40 with a load of 500 psf. By using the surcharge already on site, Menard saved the client nearly $2
million on a $10 million contract. Menard successfully installed 8,300 CMCs to support a new logistics center and ancillary buildings in Bayonne, NJ.
Print this resource