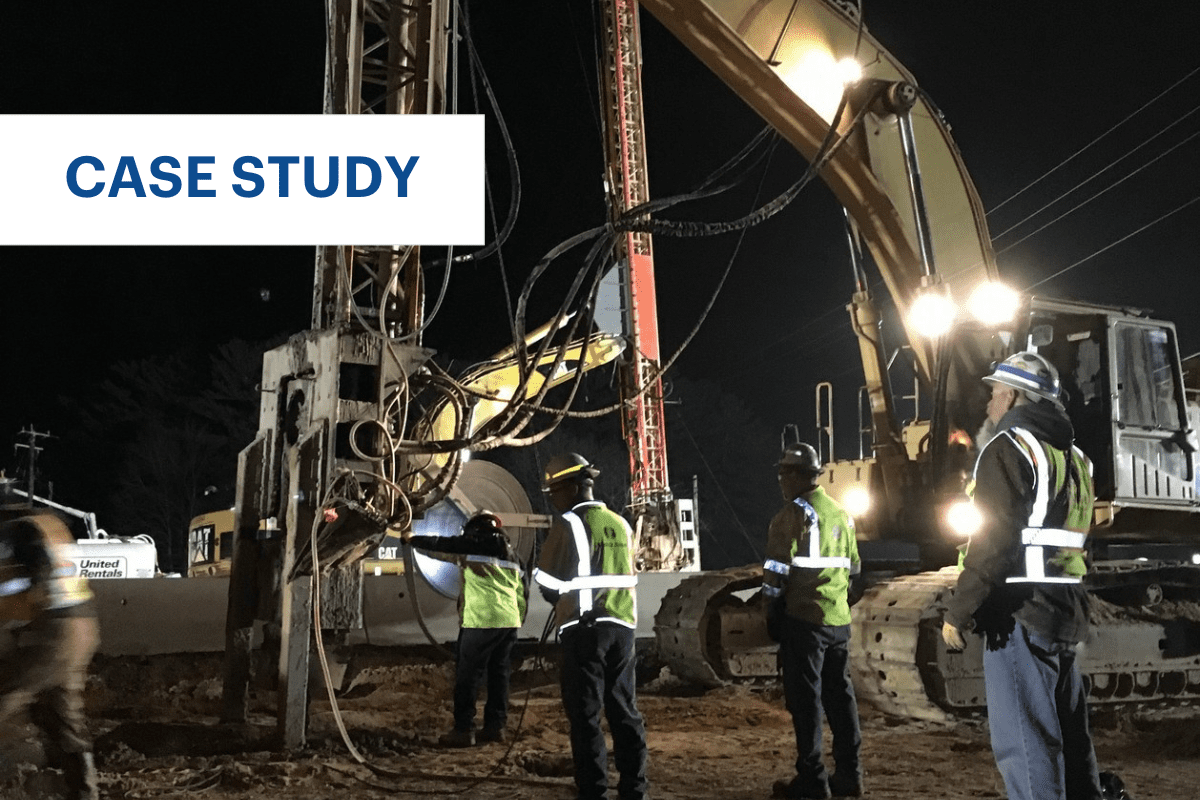
Newington Dover
Newington Dover
Project Details:
Owner: New Hampshire Department of Transportation
General Contractor: Severino Trucking Company
Date of Work: November 2016 - September 2019 in multiple phases
Engineer: NHDOT - Soils Department
Approximate Key Quantities: Controlled Modulus Column (CMC)® rigid inclusions - 269 EA and Wick Drains - 43,366 EA (2,715,040 LF)
Project Overview:
Ground Conditions:
Solution:
Auger cast piles were originally considered for support of the abutment. However, Menard provided an economical and time-saving solution with a CMC-supported Mechanically Stabilized Earth (MSE) wall. For Menard, this was its first true abutment-supported project. The CMCs eliminated the need for handling and removing large amounts of spoils generally created through the process of auger cast piles. The CMCs also terminated at an average depth of 30.8 ft and a maximum depth of 56.5 ft, significantly less than the predicted depth of the auger cast piles. Wick drains were to be installed through zero blow-count clays, with termination within the glacial outwash or on bedrock. Because of the very soft nature of the soils, Menard faced two challenges: 1) The soils were very soft at the top of the bedrock, which made it difficult to anchor the wick drains; 2) The pore water pressures were such that the wick drain anchor plate was pushed against the bottom of the mandrel (which houses the wick drain material that is hydraulically pushed or vibrated into the ground). To combat these challenges, Menard installed a water injection system at the top of the wick drain stitcher’s mast. This system filled the mandrel with water to equalize the porewater pressures in the soil, enabling the wick drains to anchor. Additionally, Menard installed CMCs to treat the soft clays and marine deposits. The elements terminated within the glacial outwash.
A total of 43,366 wick drains spanning 2.7 million LF were installed in multiple phases over three years. The drains reached an average depth of 58.6 ft and maximum depth of 125 ft. The project design provided for 2 in of post-construction settlement with less than 1 in of differential settlement, meeting the performance criteria. Menard’s solution compelled the GC to award us with three subsequent contracts for wick drain installation.
Print this resource