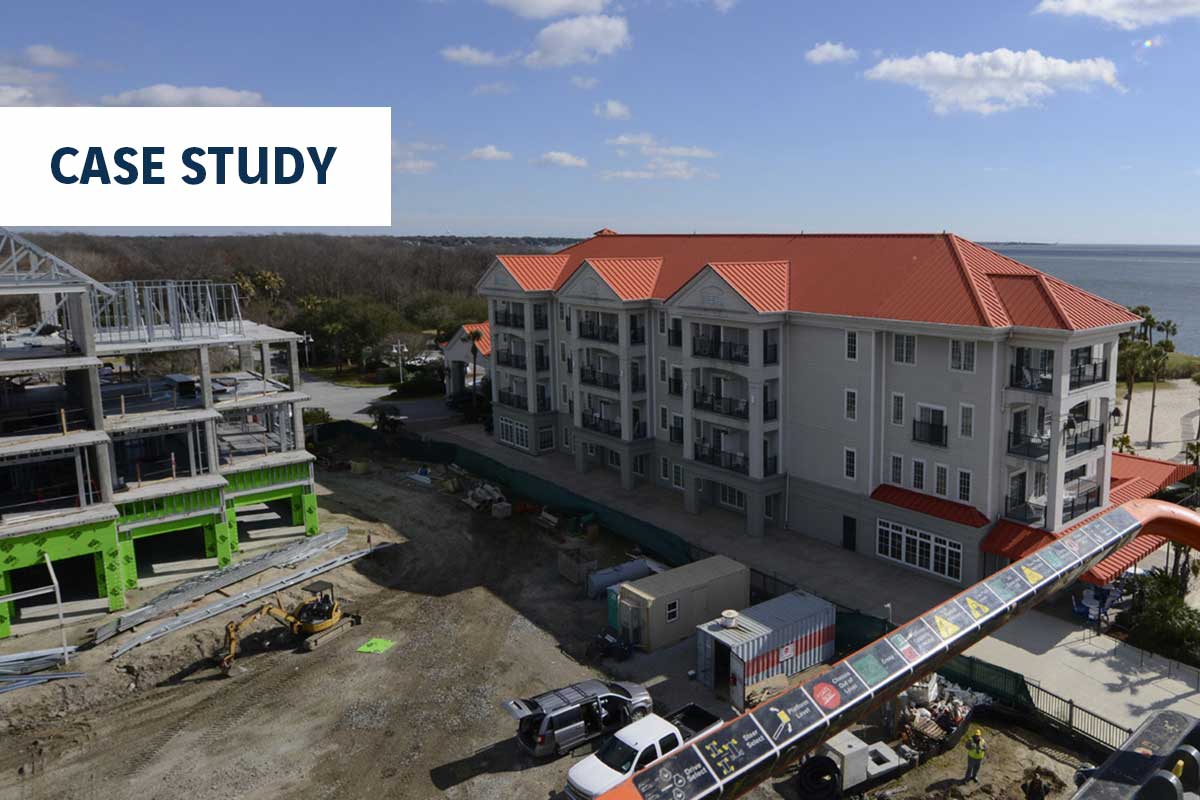
Charleston Harbor Resort Expansion
Charleston Harbor Resort Expansion
Project Details:
Owner: Brothers Property Corporation
General Contractor: Hogan Construction Group, LLC
Duration of Work: 5 weeks
Subsurface Conditions: Layers of uncontrolled fill and dredged sand over soft marine clay
Approximate Key Quantities: 620 Bi-Modulus Columns (CMC)® rigid inclusions
Project Overview:
The Charleston Harbor Resort is a boutique hotel in Charleston, South Carolina, constructed on a site with poor soils consisting of layers of dredged sand over soft marine clay. The planned four-story hotel expansion included multiple swimming pools, spas and a tiki bar that required ground improvement to support the hardscape, consolidate the soil, and minimize anticipated settlement that would occur without ground improvement. Based on the many different features needing support and the numerous cutoff depths and degrees of support required, US Wick Drain was hired to develop a solution. To meet the client and project requirements, US Wick Drain implemented Bi-Modulus Column (BMC)® as an economical and time-effective ground improvement solution.
Ground Conditions:
Solution:
US Wick Drain developed a ground improvement solution using BMCs to help strengthen, densify and compact the site’s soils. A total of 620 BMCs were installed to a maximum depth of approximately 62 feet. The client’s settlement criteria for the expansion was 1 inch total settlement and ½ inch differential settlement. The BMC design maintained these criteria and prevented further consolidation from impacting the differential settlement. US Wick Drain’s ground improvement design also saved site preparation time and costs by allowing for a single working platform elevation. The upper stone portion of the BMC facilitated the varying cutoff elevations since excavation could take place to the required depth and the hardscape features could be directly constructed upon the compacted surface.
This solution was more economical than traditional piles with pile caps and saved the client significant time due to the minimal site preparation and rapid installation of the BMCs.
Print this resource