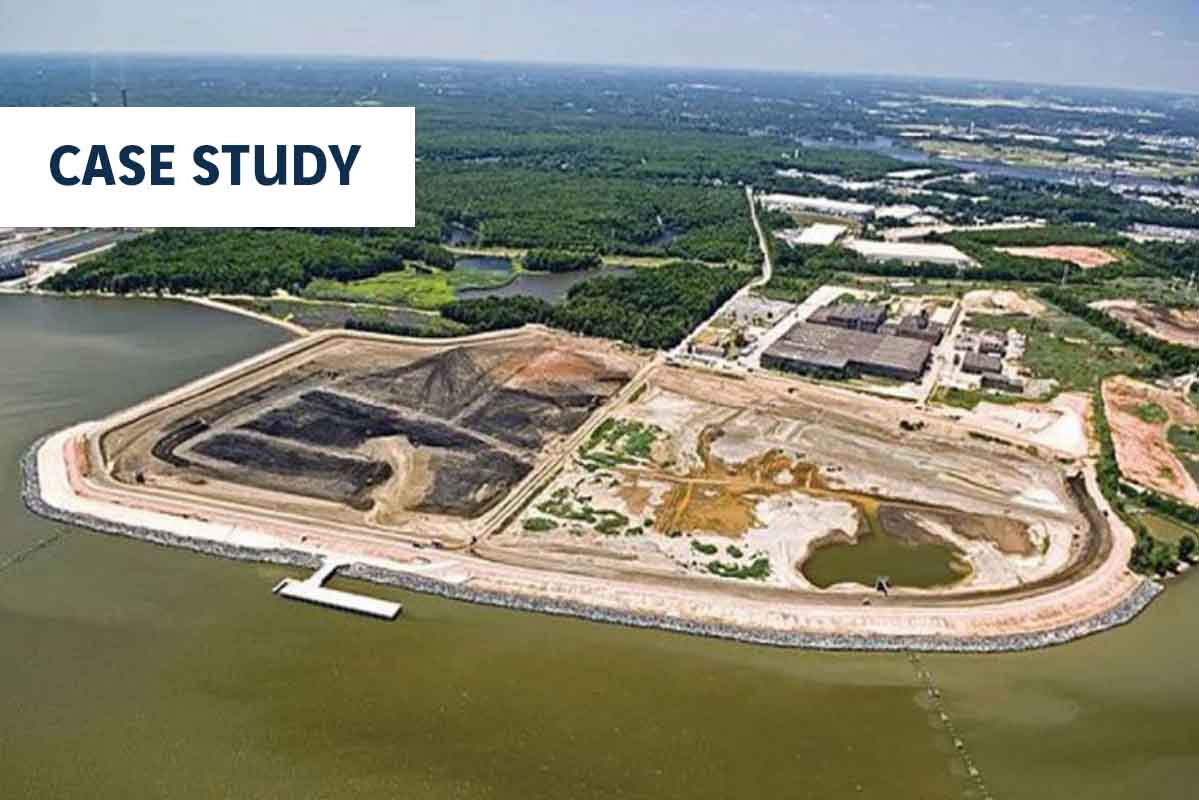
Cox Creek
Cox Creek
Project Details:
Owner: Maryland Environmental Services
General Contractor: Bowen & Kron
Dates of Work: May 2019 to December 2019
Engineer: Moffatt and Nichol
Approximate Key Quantities: Wick Drains - 61,835 EA.
Project Overview:
In Maryland, state officials approved a $116 million project to expand the Cox Creek containment facility for contaminated material dredged from the port of Baltimore’s shipping channel. The channel’s 50-ft depth, which the U.S. Army Corps of Engineers maintains by dredging, is considered crucial to the port’s continued growth as larger cargo ships start moving through the Suez and Panama canals.
The new contract, awarded to the Maryland Environmental Service under an interagency agreement with the Maryland Port Administration (MPA), would expand the MPA-owned Cox Creek site’s 133-acre dredged material containment facility onto adjacent MPA land and raise its 36-ft dikes.
Located 9 miles southeast of Baltimore on the western bank of the Patapsco River south of the Key Bridge, the site was purchased by the MPA, in parts, in 1993 and 1997. The MPA expanded the capacity for dredge material storage by strengthening and raising its dike walls. Large amounts of dredged material began to arrive in 2012.
The existing dike, with a perimeter of approximately 9,000 ft, was to be raised upwards of 25 ft and widened to accommodate future dredged material from port shipping channels. Due to the highly variable nature of soils that included dredged material/dike fill – along with soft clay and dense sand below -- Menard Group USA was contracted to support the dike expansion – the selected technique was wick drains.
Ground Conditions:
Solution:
The new dike fill was placed in controlled and monitored lifts. The wick drains acted to relieve porewater pressure which would have resulted from the addition of fill. The drains helped expedite consolidation drainage and enhanced global stability during fill placement. A total of 61,835 wick drains, at an average depth of 41 ft, were extended through the fill and soft clay into the underlying sand layer. Approximately 6,500 drains were in areas where the existing dike fill contained dense, compacted materials and required pre-augering to facilitate mandrel penetration.
Menard successfully navigated through difficult pre-augering challenges by strategically augering out front of the wick drain installation in predetermined areas. This aided in installing the 2.55 million linear ft of wick drains.
Among the site challenges overcome by Menard and the general contractor, Bowen & Kron, was the potential for UXO from a nearby bastion. No UXO were encountered during the wick drain installation. For most wick drain projects, a granular blanket is used to provide both a working surface and drainage layer to receive the water emanating from the wick drains. However, for this project, as a granular layer would potentially create a drainage pathway through the dike, there was no granular layer incorporated in the design. The fill soils were very clayey, so the working surface was not ideal. In general, installing wick drains from a clay surface should be avoided. Bowen & Kron did an excellent job maintaining the working platform, and the Menard crew took extra care to inspect the working surface in front of the wick drain operations.
To support the expansion of a dike as part of a $116 million project near Baltimore, Menard Group USA installed nearly 62,000 wick drains at an average depth of 41 ft. The drains were installed working off of a clay working surface, which is typically not a good practice. However, the general contractor worked diligently to maintain a safe working platform for the wick drain installation equipment.
Print this resource