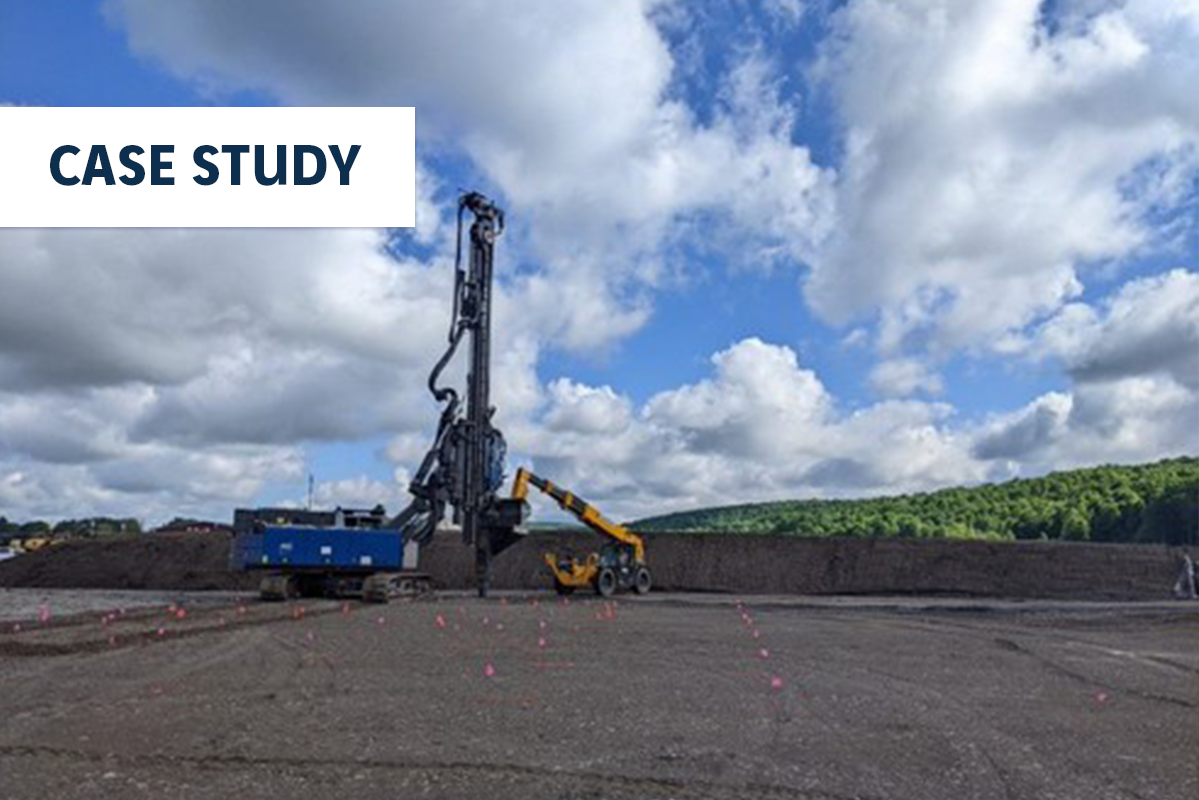
Great Lakes Cheese
Great Lakes Cheese
Project Details:
Owner: Great Lakes Cheese
General Contractor: The Dennis Group
Job Completed: June 2022
Engineer: JGA Engineering
Approximate Key Quantities: Stone Columns 527 EA.
Project Overview:
Founded in 1958 by Swiss immigrant Hans Eprecht as a cheese-delivery business in Cleveland, Great Lakes Cheese has grown exponentially – climbing to No. 132 on Forbes’ list of America’s Largest Private Companies in 2021. The Ohio-based food manufacturer distributes processed and natural cheeses – and sells imported cheeses to retailers and food service operations nationally – through eight plants, spanning five states. Great Lakes Cheese’s next endeavor is a proposed $500 million, 480,000 sq-ft facility in Franklinville, NY. The new plant, to be built on a 200-acre site along Route 98, would replace an existing plant in Cuba, NY.
The largest of Great Lakes Cheese’s eight locations, the Franklinville plant will add 200 employees to the existing 230 employees arriving from the plant in Cuba.
Due to the loose gravel fill at the site, excessive settlement was predicted. Menard USA was contracted to provide ground improvement to a “Tower Area” of the plant that would include milk storage tanks with loads ranging from 110 kips to 600 kips. The selected technique was stone columns.
Ground Conditions:
Solution:
Based on Cone Penetrometer Test (CPT) results that revealed an upper dense sand layer, Menard determined that stone columns would best improve bearing capacity by providing homogenization of the in-situ soils. Menard’s solution called for the termination of stone columns in the upper dense sand layer to support the footings. A total of 527 stone columns were installed to an average depth of 35 ft. To limit differential settlement adjacent to the unsupported floor/slab, Menard installed stone columns to approximately 10 ft beyond the limits of the supported footings. The design provided for 1 in of post-construction settlement with a ½ in of differential settlement, meeting the performance criteria of the new facility.
Menard performed a column load test using a test beam. Helical piers were installed as the reactions. The test performed within the project specifications of 1 in of total settlement. At the design load of 56 kips, the stone columns had deflected vertically 0.6 ins. At the maximum test load of 84 kips, the stone columns deflected 0.9 ins.
To support a new, 480,000 sq-ft manufacturing facility in Franklinville, NY, Menard successfully installed 527 stone columns.
Print this resource