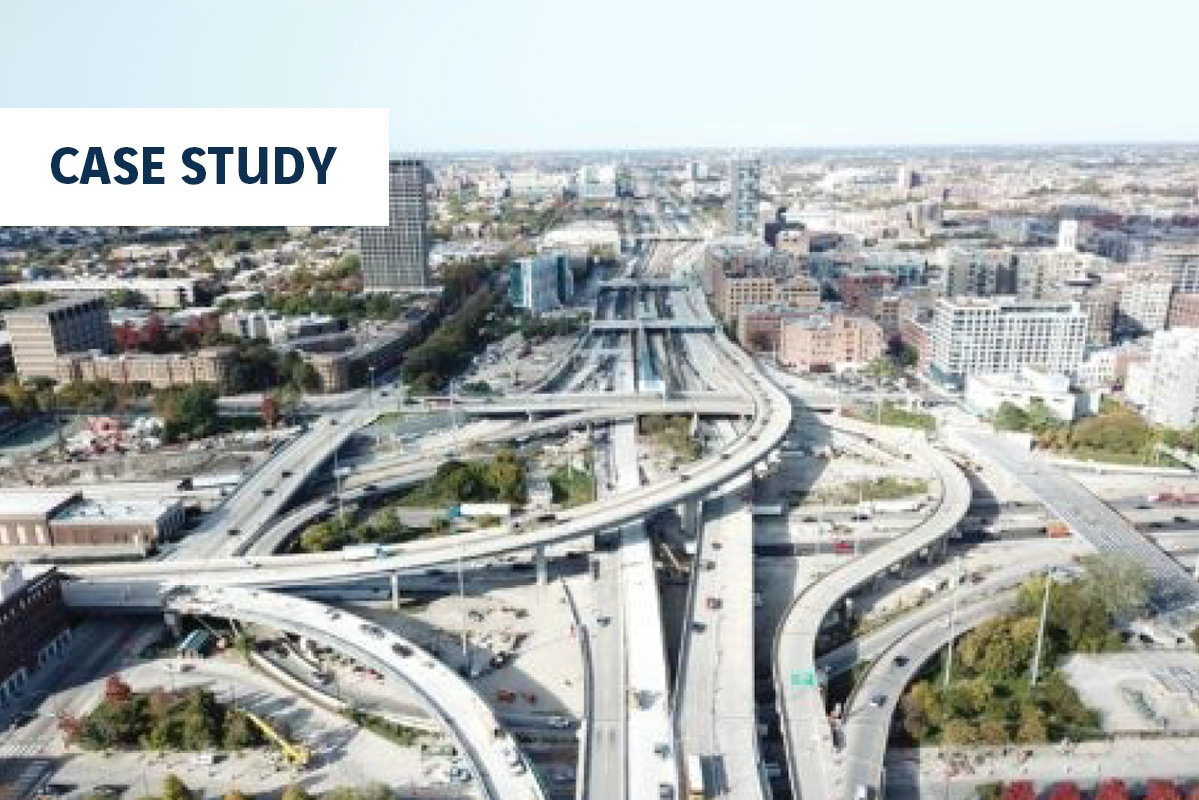
Jane Byrne Interchange
Project Details:
Owner: Illinois Department of Transportation
General Contractor: Lorig Construction Company
Duration of Work: 4 weeks
Subsurface Conditions: Soft to very soft clay underlying surficial stiff loam fill. A layer of very stiff clay existed below this layer, overtop of dense glacial til.
Approximate Key Quantities: 126 stone columns
Project Overview:
The Jane Byrne Interchange (formerly the Circle Interchange) is a major freeway interchange near downtown Chicago. Opened in the 1960s, it is the junction between Interstate 90/Interstate 94, Interstate I-290 and Ida B.Wells Drive. In a dedication ceremony in August 2014, the interchange was renamed in honor of former Chicago Mayor Jane M. Byrne. Notorious for its traffic issues, it was rated as the country’s third-worst traffic bottleneck, with drivers of approximately 300,000 vehicles daily losing a combined 25 million hours each year. Beginning in 2013, the Illinois Department of Transportation (IDOT) began a methodical process of reconstruction involving 35 separate contracts spread over nine years. One of the contracts involved the relocation of various ramps and the placement of new fill to form these embankments. To save space in the congested interchange, Mechanically Stabilized Earth (MSE) walls were utilized to retain this fill, rather than slopes.
Due to the compressible nature of the soils at the site, Menard USA was contracted to install stone columns to support the two, 25-ft tall MSE walls.
Ground Conditions:
The soil profile consisted of several ft of surficial stiff loam fill. Underlying this layer was a thick layer of primarily soft to very soft clay as deep as 45 ft. A layer of very stiff clay existed below this layer, overtop of dense glacial till, known as the Chicago hardpan layer.
Solution:
Menard’s proposal to install stone columns for support of the MSE walls was both economical and time-saving as compared to other bids/approaches. In less than one month, Menard installed 126 stone columns (42-in in diameter) to an average depth of 20 ft. The design provided for 1 in of post-paving settlement, meeting the performance criteria of the project. In using lightweight fill for the MSE walls, an equivalent maximum bearing pressure of 1,400 psf was applied to the base of the wall. The stone columns were designed exclusively for settlement control, as bearing capacity was ensured by the use of the lightweight fill.
Of note: Due to the required construction sequence, work was done beneath an existing overpass. This low-overhead condition limited the depth of installation to 20 ft, which only partially treated the soft soil. This partial treatment, in combination with the lightweight fill used in the MSE wall, resulted in an optimized overall design. In addition to reducing the settlement, the stone columns also accelerated the settlement due to their high permeability, which allowed for faster paving of the ramps. A major challenge at the site was the presence of soft soil – which made it difficult to construct a suitable working platform. Menard worked closely with the general contractor to ensure work could proceed safely and productively. Another challenge was the occurrence of heave due to the installation of the large-diameter stone columns. Proper construction sequencing and coordination with the earthwork contractor to remediate soft spots on the site were critical to ensure a quality product and safe platform.
Notwithstanding all challenges, Menard successfully installed 126 stone columns to support two MSE walls as part of a major highway project in Illinois.
Print this resource