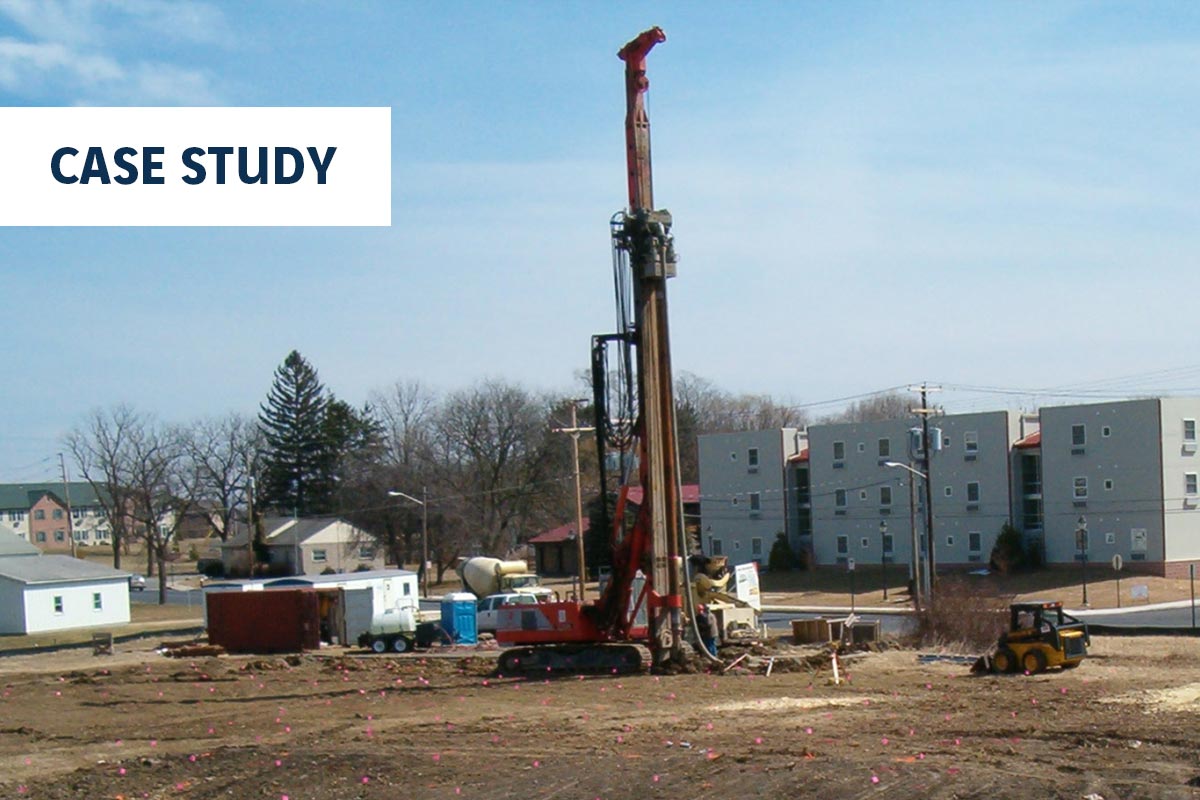
Kutztown University
Kutztown University
Project Details:
Owner: Kutztown University
General Contractor: The Quandel Group
Duration of Work: 1 week
Subsurface Conditions: Very loose fill of variable thickness and silty sand with gravel
Approximate Key Quantities: 250 Controlled Modulus Columns (CMC)® rigid inclusions
Project Overview:
The proposed Kutztown University dormitory building was to be built on a site with soils that were unsuitable for the construction of such a structure. The building is a three-story masonry shear wall dormitory on two foot wide strip footings and slab-on-grade. The loads imposed by the dormitory would have created unacceptable settlement of the uncontrolled fill soils at depth. Although several ground improvement options were available to the client, Menard was able to develop an alternative approach of Controlled Modulus Columns (CMC)® rigid inclusions, that saved the client both time and money.
The footing elevations were below the proposed working surface and set at varying elevations. Accordingly, the ground improvement design and installation would need to accommodate the low cutoff of ground improvement elements or inclusions.
Ground Conditions:
Solution:
The CMC rigid inclusion elements were designed using proprietary software developed by Menard, creating a solution that reduced settlement to within design specifications.
Menard installed 256 CMC rigid inclusions to depths ranging from 11 to 14 feet using a specially-designed auger that displaces the soil laterally, with very minimal spoils created. Menard was able to accommodate the client’s requirement to cut the elements off at depths up to 5 feet below working surface. This was accomplished by employing specially developed tools and auguring techniques that left the top of each element at the client’s desired elevation.
Print this resource