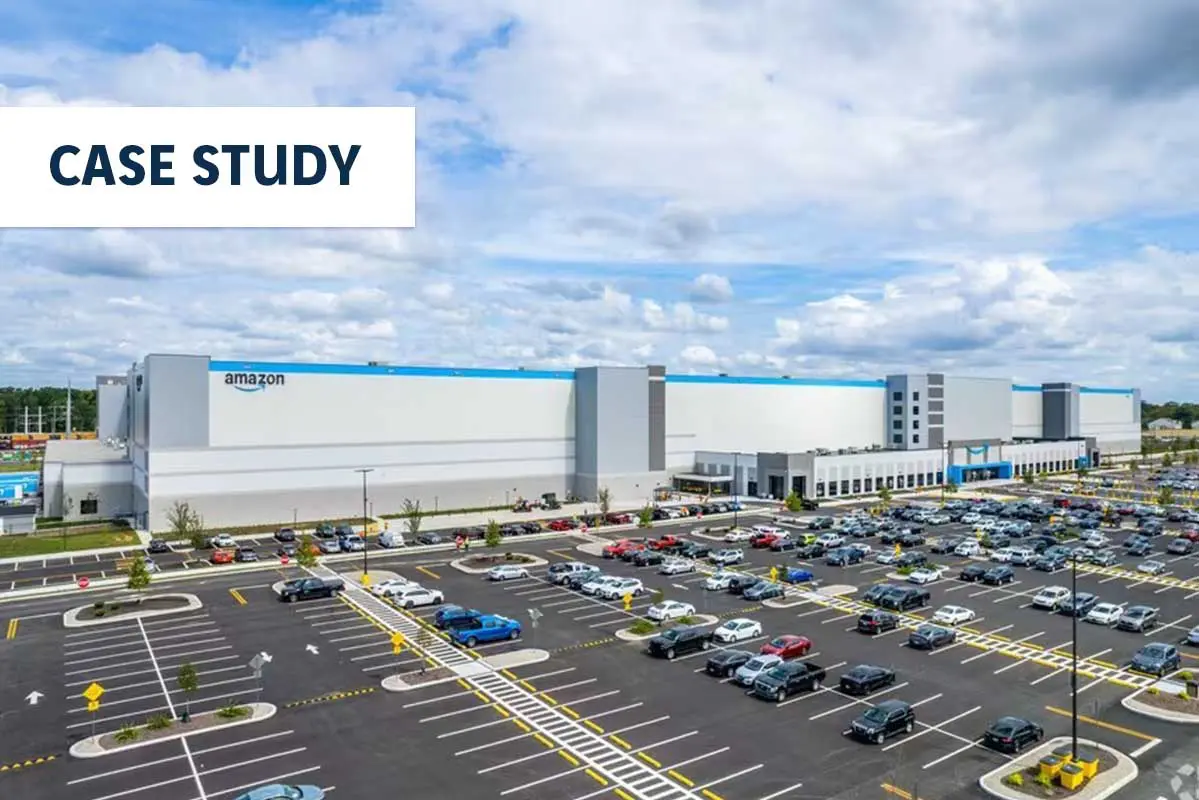
Project Sophia
Project Sophia
Project Details:
Owner: Amazon
General Contractor: Clayco Corporation
Dates of Work: February 2020 - May 2020
Engineer: Langan Engineering
Approximate Key Quantities: CMCs - 4,603 EA.
Project Overview:
Due to the variability in soil stiffness/type over the warehouse footprint, ground improvement was required to prevent differential settlement and improve bearing capacity for the foundations. To further identify the soil properties at each footing location and design a unique ground improvement solution that fit the loading condition and soil profile, Menard proposed an additional investigation that included a series of Cone Penetrometer Tests (CPT). Controlled Modulus Column (CMC)® rigid inclusions were ultimately selected to support the new warehouse.
Ground Conditions:
Solution:
Ground improvement utilizing stone columns or rigid inclusions was recommended for foundation support. Given the variability in soil conditions, the “one size fits all” approach was not economical or technically sound. Given this challenge, Menard’s CPT investigation included every column location. This was done to properly identify the soil profile. Evaluation of the CPT results concluded a robust ground improvement program would be required. CMCs were chosen as the solution. Menard classified each soil profile as “good” or “bad.” A pre-design footing analysis for both soil conditions determined the amount of CMC support required for each individual footing. This ensured that each footing would receive the correct amount of CMC support, while alleviating concerns for differential settlement between the column bays. While the CPT investigation and CMC installation were being performed, close coordination was required between Menard design engineers and the field crew to ensure CMC locations and depths were communicated in a timely manner to prevent delays.
This project highlights Menard USA’s ability to not only adapt to a fluid project, but a geotechnically challenging environment. With an abbreviated bid timeline and incomplete information, a plan was developed to ensure the client’s schedule and technical obligations were met in a fast-paced environment. Menard successfully installed 4,600 CMCs to support a new Amazon warehouse in Wilmington, DE.
Print this resource