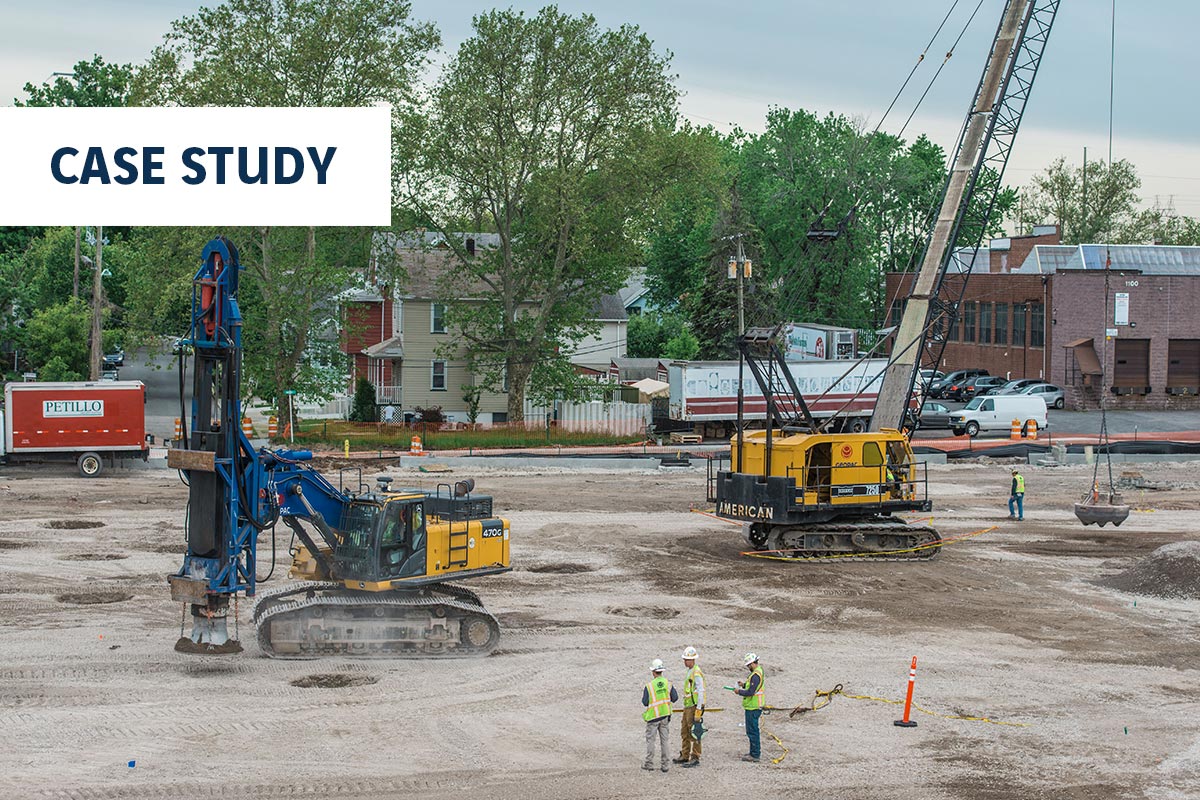
Metro Point – One Bell Drive
Project Details:
Owner: Sitex Group
General Contractor: RC Andersen, LLC
Duration of Work: 6 weeks
Subsurface Conditions: Upper layer of historic fill over a layer of soft, highly compressible organic peat
Approximate Key Quantities: 560 prints of Dynamic Compaction, 1,900 prints of Rapid Impact Compaction, 1,066 Controlled Modulus Column (CMC)® Rigid Inclusions
Project Overview:
One Bell Drive is an industrial complex located in Ridgefield, New Jersey that is composed of two new distribution warehouses. Investigations of the site’s soils revealed an upper layer of historic fill over a layer of soft, highly compressible organic peat. The presence of the organic peat layer was of great concern to project engineers due to the large settlements that were expected to occur following the construction of the two warehouses. The concerning soil layers also varied in thickness between the two sites of the proposed warehouses. To reduce anticipated settlement and improve the unique ground conditions under each warehouse foundation, Menard proposed an innovative ground improvement solution that combined several proven techniques, including Controlled Modulus Column (CMC)® rigid inclusions, dynamic compaction (DC) and rapid impact compaction (RIC).
In addition to these techniques being an economical alternative to aggregate piers and traditional pile support,they were implemented simultaneously which saved the client considerable schedule duration.
Ground Conditions:
The larger warehouse covered an area of approximately 195,000 sq. ft and the fill layer extended from 0 to 8 ft below the existing grade. Below the fill was a thin layer of soft organic peat extending from 8 to 10 ft, and underneath the organic peat layer was a stratum of silty sand from 10 to 60 ft grading from loose to medium dense to dense. The thin organic layer was present in small quantities and not close to the surface.
The smaller warehouse covered an area of approximately 83,000 sq ft. While the general soil profile at this location was similar to that of the larger warehouse, the organic peat layer was thicker and closer to the surface at a depth of 5 to 8 ft below grade.
Solution:
For the larger warehouse Menard originally proposed DC. However, the effects of vibrations associated with DC on a nearby residential neighborhood became a concern after Menard’s initial proposal was offered. Menard found that the incorporation of RIC would impart enough energy into the soil to provide adequate densification while minimizing disturbances to the residential neighborhood.
Several ground improvement options were considered for the construction of the smaller warehouse, including aggregate piers and piles. CMC rigid inclusions were selected as the most appropriate solution to improve the soil based on Menard’s experience with similar projects, construction schedule, and cost-effectiveness. The presence of the thicker, organic layer made DC and RIC a less desirable option for ground improvement because a surcharge and waiting period would have been needed to increase the rate of settlement of the compressible materials. Menard’s solution of CMC rigid inclusions to improve the ground saved the client money over traditional foundations, such as piles, and was a better technical fit than aggregate piers. The CMC rigid inclusions could also be installed in the vicinity of an existing utility line that was sensitive to vibration. Menard installed more than 1,000 CMC rigid inclusions at depths up to 42 ft to support the foundation of the smaller warehouse.
This project required the coordination of multiple techniques to be implemented simultaneously, in complex soil conditions and over large areas. Secondary settlement of the organic peat layer was of concern and was addressed in Menard’s design. Confirmatory borings for the larger warehouse and a load test for the CMC rigid inclusions in the smaller warehouse were performed to verify the design parameters.
Print this resource