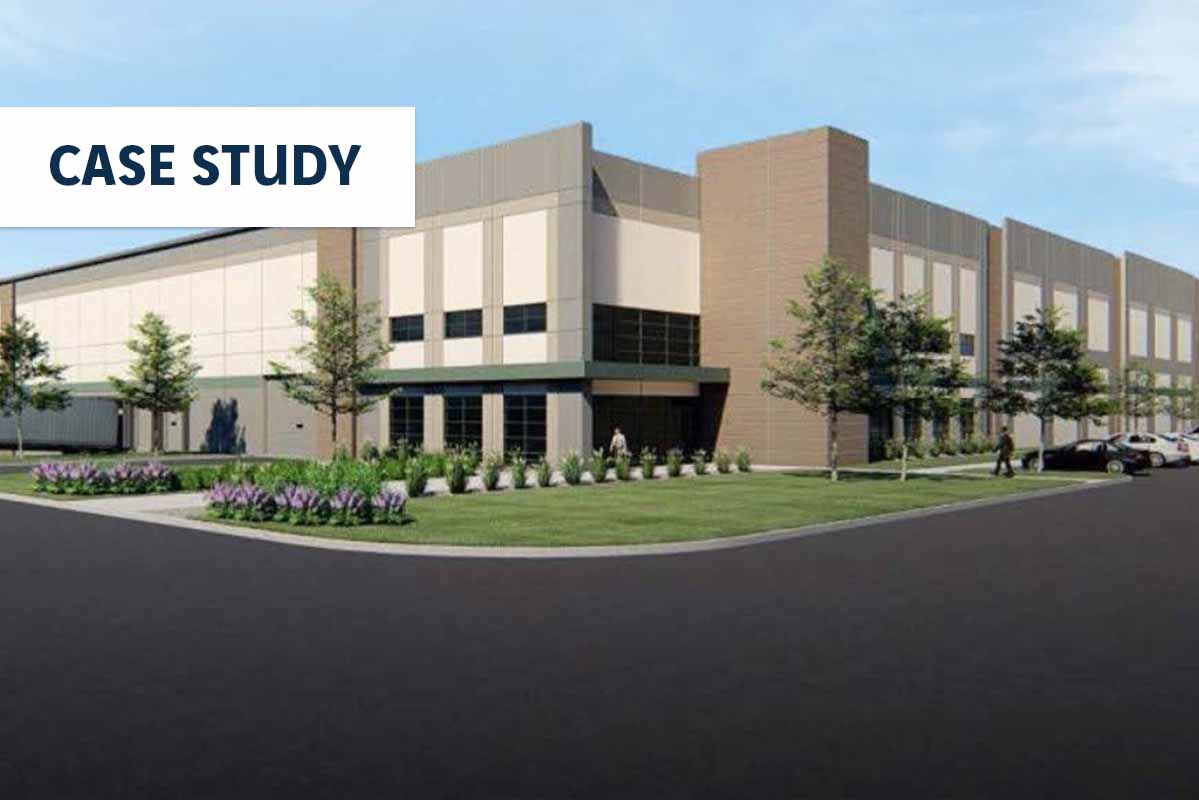
Oakland Logistics Park
Oakland Logistics Park
Project Details:
Owner: Flint Development
General Contractor: Brinkmann Constructors
Job Completed: July 2021
Engineer: Testing Engineering & Consultants (geotechnical); Krudwig Structural Engineers
Approximate Key Quantities: Stone Columns 600 EA.
Project Overview:
As part of Flint Development’s efforts to construct 2.3 million sq. ft of speculative bulk warehouse space in the Detroit Metro Region, a 711,360 sq-ft warehouse was proposed for the sprawling site. The Oakland Logistics Center – with 36-ft clear-height ceilings and 150 trailer spaces – would meet the needs of a changing economy while contributing to one of the largest speculative projects in Michigan.
The project location, Oakland Logistics Park in Pontiac, once housed an automotive assembly plant. During previous construction, fills of up to 10 ft were placed with varying degrees of compaction -- and deemed insufficient for bearing capacity and settlement control of the new construction. The geotechnical engineer
recommended stone columns as a means of ground improvement – and Menard USA was selected to design and install the elements.
Ground Conditions:
Solution:
Drilled piers were originally considered for the foundation system, but due to the variable bearing layer and cost of installation, they were eschewed for stone columns. The elements were installed through the fill soils and designed to provide 3,000 psf of bearing capacity while limiting settlement to 1 in. Slabs were constructed on-grade following a proof-roll. Menard installed 600 stone columns to depths of up to 15.5 ft, and performed two load tests to confirm the stone column modulus assumed during the design phase. Frequent and severe rain events caused delays, but Menard worked with General Contractor Brinkmann Constructors to work in dry areas of the site to maintain schedule. The rain also meant that more areas showed the perched groundwater, prompting Menard to switch from a top-feed installation to a bottom-feed installation to properly construct the stone columns in the wet conditions.
For an expansive, speculative bulk warehouse project in Pontiac, MI, Menard installed 600 stone columns to support a 711,000 sq-ft warehouse.
Print this resource