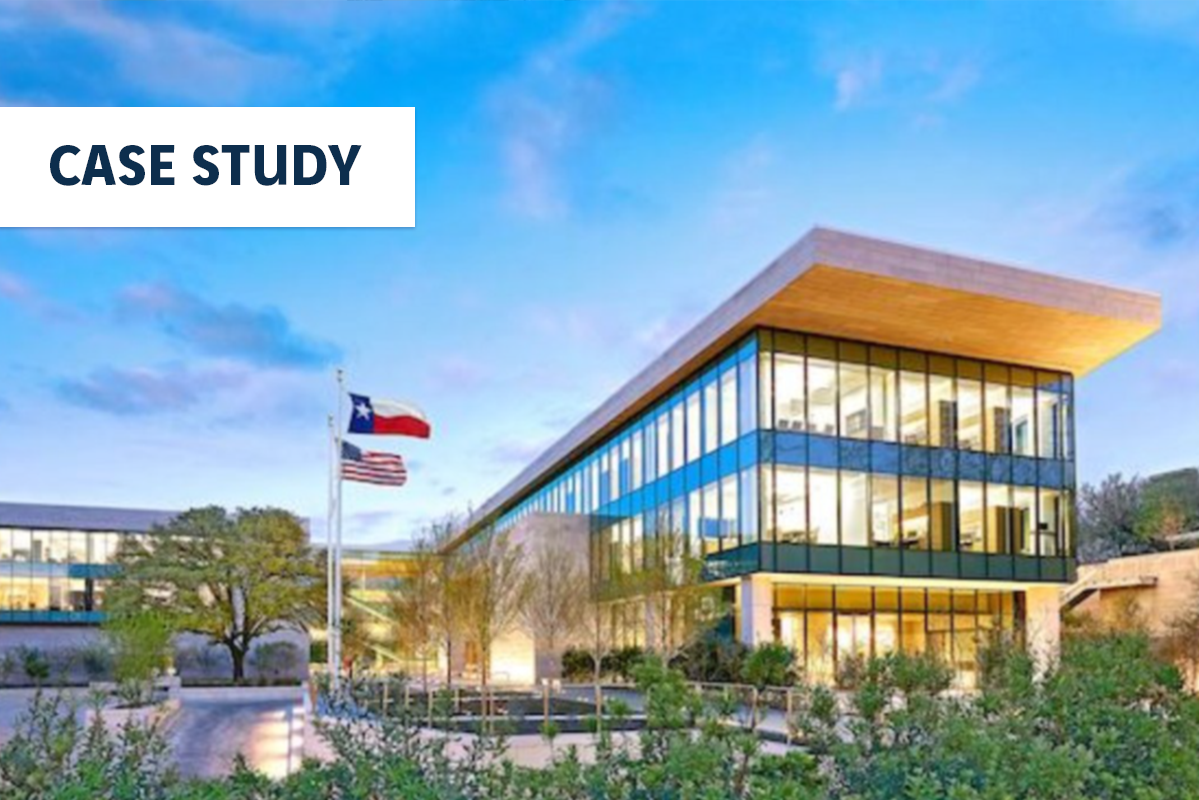
Project Speedway
Project Speedway
Project Details:
Owner: Confidential Client
General Contractor: Clark Construction Group
Job Completed: October 2021
Engineer: HSA & Associates
Approximate Key Quantities: Controlled Modulus Columns (CMC)® - 4,250 EA. | Wick drains - 3,962,000 LF
Project Overview:
Nicknamed the “Action Track,” Richmond Raceway in Henrico County, VA, is a staple on the NASCAR Cup Series. Fans flock to the venue, in part, for its grooved “D” shaped track, which enables drivers to reach high speeds. The raceway once sold out 33 consecutive events. Adjacent to this lively venue, a 650,000 square-foot robotics fulfillment center was proposed by a major e-commerce company on 119 acres in Henrico’s Fairfield District. The new facility would create upwards of 1,000 jobs for the region.
Due to the nature of the soils at the site, Menard USA, an international specialty ground improvement contractor, was contracted to provide ground improvement. The selected techniques were Controlled Modulus Column (CMC)® rigid inclusions and wick drains.
Ground Conditions:
Solution:
Initially, aggregate piers, CMCs and wick drains were considered for ground improvement. The biggest challenge -- due to the placement of new fill -- was the potential for settlement issues in the soft and compressible alluvial and marine deposits. Menard designed a solution implementing wick drains and shallow CMCs to meet the project’s needs. As the project progressed, the slab load changed from 150 psf to 500 psf and the total settlement tolerances changed from 1.5 inches to 1 inch. The column loads also increased. This required a design modification, from a shallow CMC solution to a deep CMC solution.
For the slab, wick drains were installed under the building to accelerate fill settlement (from a projected 3-5 years to 40-50 days). Wick drains were also used outside the building footprint in areas requiring the placement of new fill. The fill was as high as 30 feet in some areas.
Menard’s modified CMC solution provided the required bearing capacity, while reducing the settlement of the footings. Menard originally designed for CMC installation to depths of 45 feet, but the discovery of compressible soils at depths of 100 feet in addition to the changes in the loading conditions resulted in CMC installation depths up to 85 feet.
Menard installed 4,250 CMCs, totaling 340,000 LF, to a maximum depth of 85 ft. Menard also installed 3,962,000 linear feet of wick drains as to support the new structure. CMCs were designed to achieve a bearing capacity of 6 ksf at each footing with column loads up to a maximum of 3000 kips. The wick drains accelerated the timeline of settlement for the slab, which was designed for uniform loading of 500 psf. The design provided for 1 in of post-construction settlement with a differential settlement of less than a 1/2 in, meeting the performance criteria of the building.
For a 650,000 square-foot facility in Henrico, VA, Menard USA installed 4,250 CMS and 3.9 million linear feet of
wick drains.
Print this resource