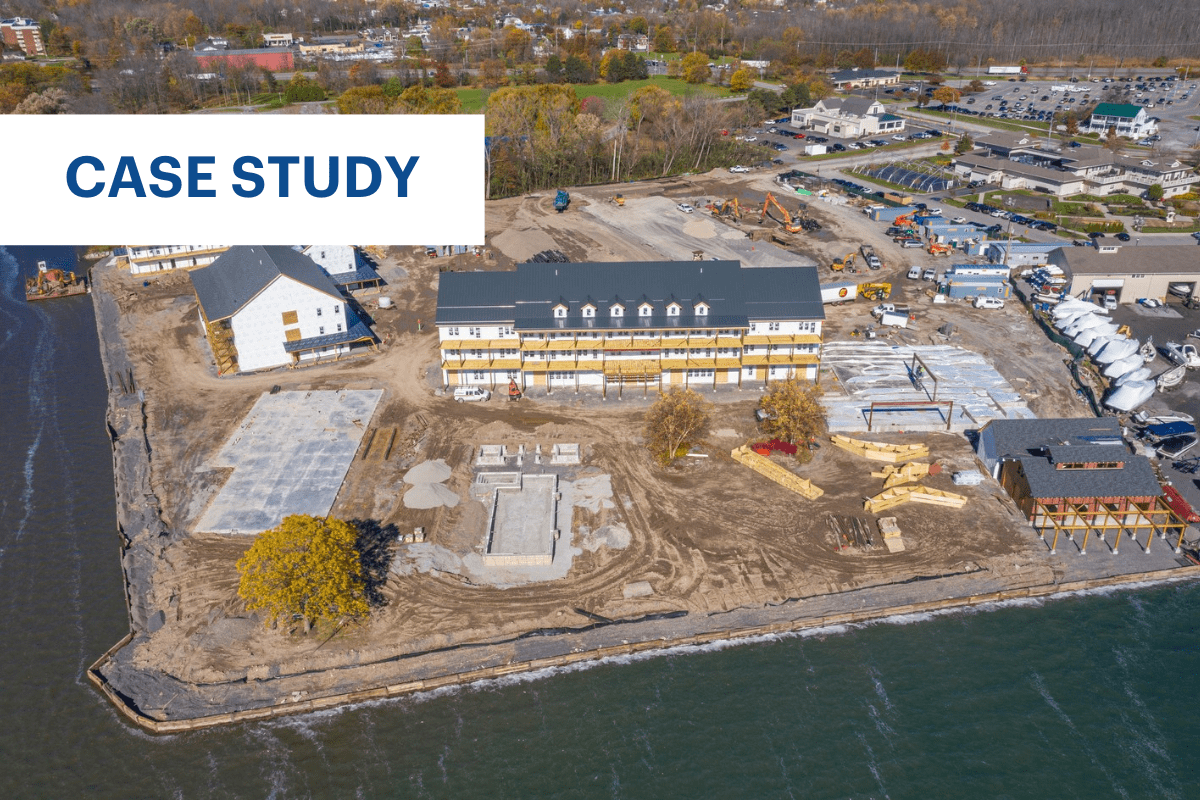
The Lake House on Canandaigua
The Lake House on Canandaigua
Project Details:
Owner: L,R, R M NY, LLC
General Contractor: LeChase Construction
Dates of Work: April 2019 to May 2019
Engineer: Foundation Design, PC
Approximate Key Quantities: Controlled Modulus Columns - 954 EA.
Project Overview:
Ground Conditions:
Solution:
Helical Piers were originally proposed to terminate in the upper stiff clay formation from 15-20 ft below grade. Pile tests, however, determined that the Helical Piers did not provide adequate support and would need to be extended to the dense glacial till layer at 55 ft below grade. This prompted the owner and engineer on the project to propose CMCs as an alternative form of foundation support. CMCs would provide considerable savings, given the cost of installing concrete (CMCs) to an average depth of 55 feet is more economical than installing steel helical piers to the same depth.
A challenge Menard faced was high ground water, which made it difficult to achieve compaction of the Load Transfer Platform (LTP). The LTP is a compacted stone layer that acts as a cushion between the top of the CMCs and the foundations. To overcome this concern, Menard’s design team innovatively incorporated flowable fill to allow for LTP placement to overcome the high groundwater table.
The design provided less than 1-in of post-construction settlement with less than a ½-in of differential settlement, meeting the Engineer’s performance criteria for the building. Menard installed 954 CMCS to an average depth of 52 ft and maximum depth of 62 ft. Menard’s ground improvement solution of CMCs supported the construction of a four-story hotel that has emerged as one of the premier destinations in the US.
Print this resource