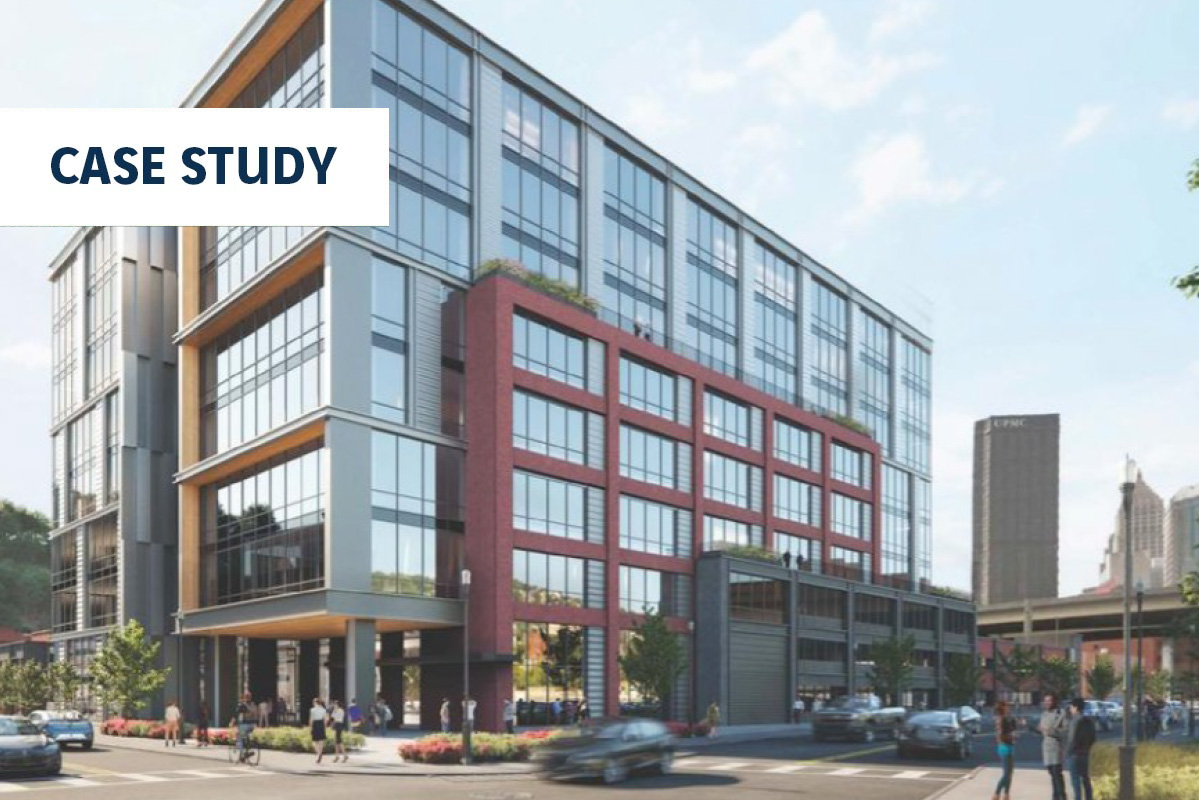
Vision on Fifteenth Street
Project Details:
Owner: Burns Scalo Development, LLC
General Contractor: Burns Scalo Development, LLC
Duration of Work: 4 weeks
Subsurface Conditions: Below the fill is a soft silty clay layer followed by a dense sand and gravel layer.
Approximate Key Quantities: 759 Controlled Modulus Column (CMC)® rigid inclusions
Project Overview:
An eight-story, $75 million building with office, retail and restaurant space was proposed for the historic Strip District in Pittsburgh, PA. Known as The Vision on Fifteenth, the future 275,000 sq-ft structure would offer tenants oversized floorplans, terrace views of Downtown Pittsburgh and the Strip District, an interactive lobby video wall and state-of-the-art fitness amenities including direct access to outdoor recreational activities and an indoor rock-climbing wall.
The development also would feature a multi-modal transportation component featuring 390 parking spaces, 90 bike storage spaces, 20 electronic vehicle charging stations, and a bike/electric scooter sharing program.
Due to the compressible nature of the soils at the site, Menard USA was contracted to provide ground improvement – the selected technique was Controlled Modulus Column (CMC)® rigid inclusions.
Ground Conditions:
The soil consisted of 10-17 ft of silty clay fill with a number of large obstructions. The fill was removed and replaced by the general contractor before Menard mobilized. Below the fill is a soft silty clay layer reaching depths of approximately 30 ft, followed by a dense sand and gravel layer (which served as the bearing layer for the CMCs).
Solution:
Augercast piles were originally considered for support of the new building. However, Menard provided an economical and time-saving solution with CMCs. Menard’s solution included 759 elements installed to an average depth of 34 ft and a maximum depth of 39 ft. Some CMCs were reinforced to account for lateral loads and bending moments.
The design provided for 1 in of post-construction settlement with less than a ½-in of differential settlement, meeting the performance criteria of the new, multi-use development. Two load tests were performed to confirm the capacity of the CMCs both in compression and tension.
The schedule for this project was accelerated, in large part, because Menard employed pre-drilling to penetrate the compacted, placed fill.
Because work was done in an urban setting, often during business hours, noise, vibration and general impact from construction had to be kept to a minimum. Menard deftly navigated through these challenges, successfully meeting the client’s requirements for quality, safety and schedule and allowing the client to eliminate augercast piles and realize significant savings in concrete by using spread footings in lieu of pile caps.
Print this resource