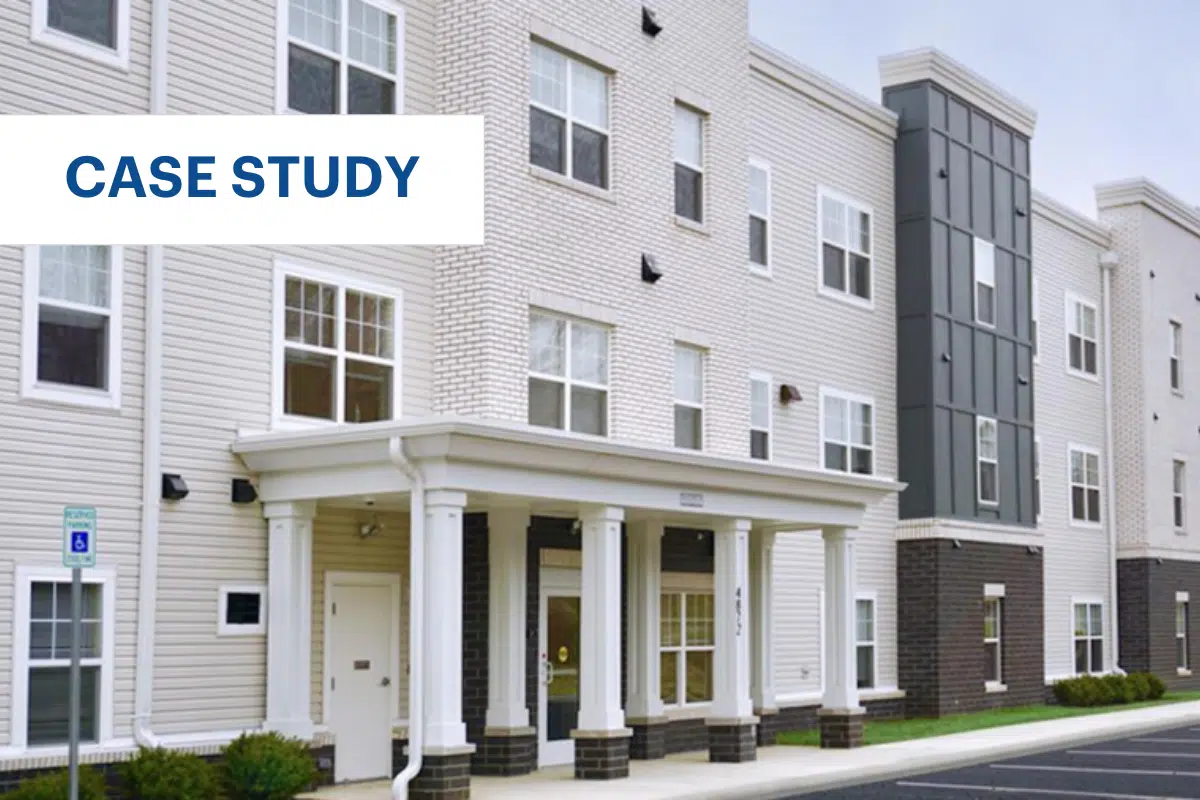
Wendler Commons
Wendler Commons
Project Details:
Owner: Wendler Commons Limited Partnership
General Contractor: Woda Construction, Inc.
Date of Work: March 2020 - April 2020
Engineer: Structure Point
Approximate Key Quantities: Controlled Modulus Columns (CMC)® - 707 EA.
Description:
The construction of two apartment buildings with surface parking lots for each building was proposed in the northeast side of Columbus, OH. The $13.8 million Wendler Commons project would provide affordable housing near major job centers, including Limited Brands headquarters and logistics centers, with more than 10,000 employees across three shifts. The three-story, 12,000 sq-ft townhouse-style buildings would consist of 62 units. The park-like setting would feature a conservation area with natural features and tree buffers, ample parking and outdoor recreation areas.
Income levels for future residents was projected to range from $16,050 to $42,800 for single-person households, and up to $61,120 for a four-person household. The goal was to provide easy access to jobs near employment centers. Tax credits were provided to developers by the Ohio Housing Finance Agency.
Due to the soft and compressible nature of the soils at the site, Menard USA was contracted to provide ground improvement for the new apartments and the surface parking lots – the selected technique was Controlled Modulus Column (CMC)® rigid inclusions.
Ground Conditions:
Solution:
The initial foundation system was designed for drilled shafts. Estimates for the drilled shafts were high and were considered cost prohibitive. Aggregate piers were also evaluated for ground improvement but were ruled out due to the potential of excessive settlement in the very soft clay. Menard provided an economical and timesaving solution by installing 707 CMCs to an average depth of 25 ft and a maximum depth of 27 ft. This saved the client approximately $300,000 from the drilled shaft price estimate.
The building foundations were designed for a bearing stress of 3 KSF. The design targeted 1 in of post-construction settlement with less than a ½-in of differential settlement.
The site was located in low topography, adjacent to a wetland area, which resulted in poor drainage and an unstable work area. This required additional thickness of working pad to support production equipment. The load transfer platform (LTP) design considered the very soft clays and required additional thickness to transfer the building loads into the CMCs. An additional challenge was the COVID-19 pandemic which began shortly after we mobilized to the site, forcing a 10-day shutdown after several days of production. Once crews returned to the site, Menard successfully completed work and supported two apartments and two surface parking lots, saving approximately $300,000 as compared to the original drilled shaft foundation system.
Print this resource