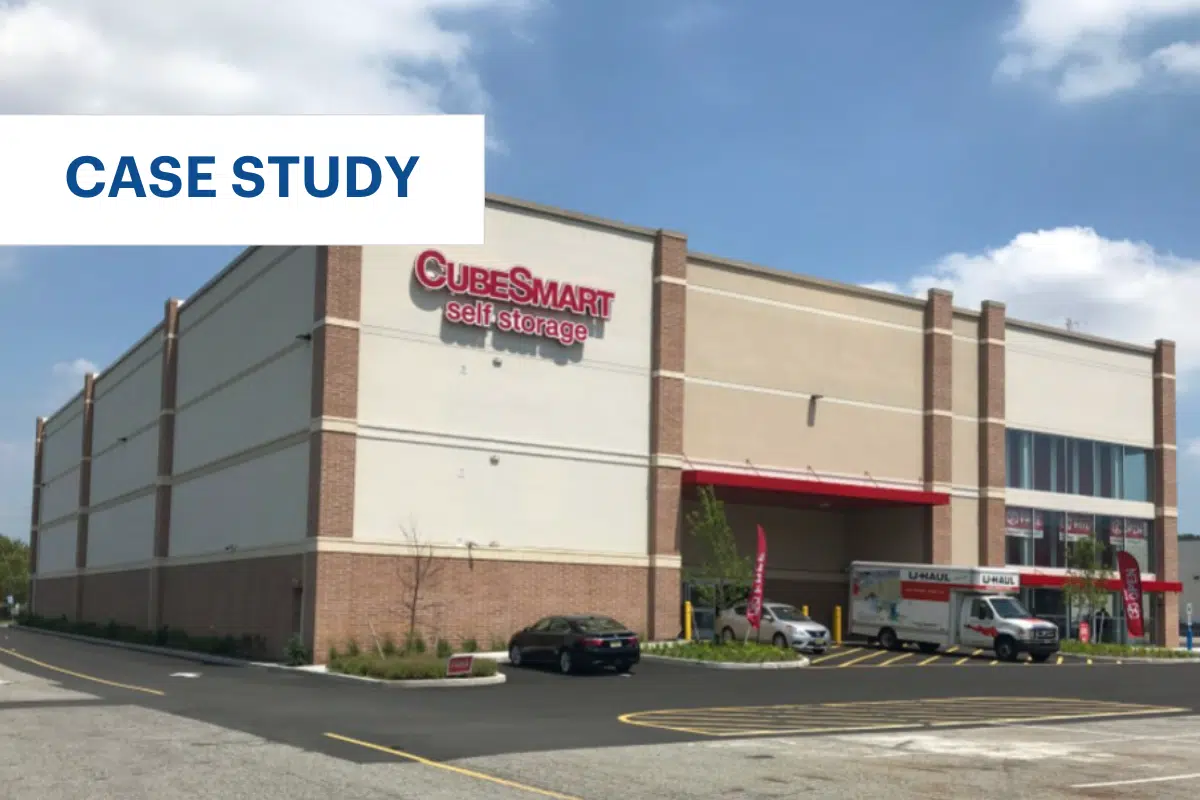
CubeSmart
CubeSmart
Project Details:
Owner: Urban Edge Properties
General Contractor: A&E Construction
Date of Work: June 2018 - July 2018
Engineer: Langan Engineering & Environmental Services
Approximate Key Quantities: Controlled Modulus Columns (CMC)® - 314 EA.
Description:
Ground Conditions:
Solution:
Micropiles were initially considered for support of the storage facility. However, Menard provided an economic and timesaving solution with CMCs. Not only were CMCs installed to shallower depths than what would have been required for micropiles, but they also provided a savings of between $250,000 and $400,000 to the client. Menard installed 314 CMCs to an average depth of 70 ft and a maximum depth of 79 ft. The CMCs were designed with a maximum capacity of 120 kips each. The general contractor removed boulders and obstructions from the fill layer in areas.
The CMC rigid inclusion installation under all spread footings served to take the load through soft soils allowing for spread footings and slab-on-grade construction. Steel fiber reinforcement supplied by Bekaert was used to enhance the strength of the slab. While Menard has worked with Bekaert on several projects, this was the first time that the companies designed a fiber-reinforced slab for a self-storage facility. The use of CMCs was crucial in minimizing generation of contaminated soils. The CMC design provided for 1 in of post-construction settlement, with less than a ½ in of differential settlement, meeting the performance criteria of the new facility.
Menard and Bekaert worked together to provide a CMC-supported fiber-reinforced slab for a new storage facility at a site with heavily obstructed soils.
Print this resource