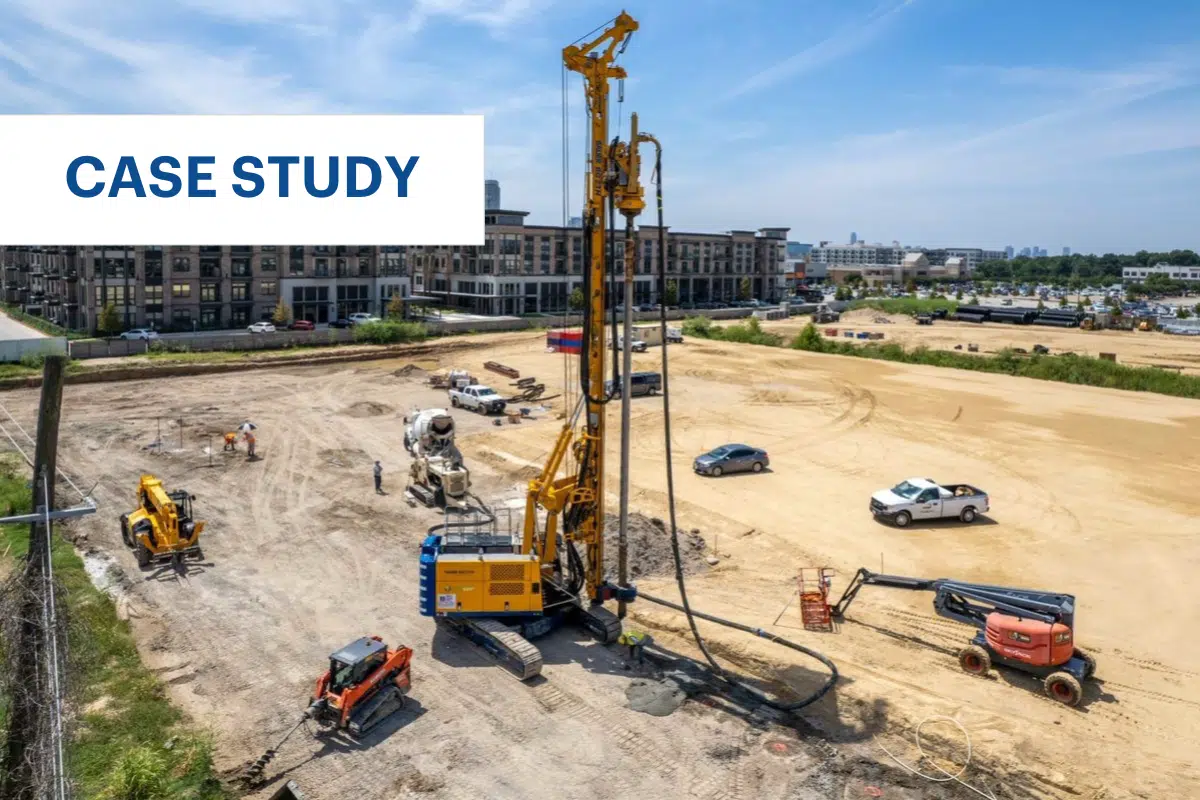
Lower Heights District (LHD) Home Depot
Lower Heights District (LHD) Home Depot
Project Details:
Owner: Gulf Coast Commerical Group
General Contractor: LaGrone Servies, Ltd.
Date of Work: September 2021
Engineer: Kimley Horn (Civil); Northwest, Inc. (Structural)
Approximate Key Quantities: Controlled Modulus Columns (CMC)® - 453 EA.
Description:
A multi-phased mixed-use development was proposed for the 24-acre Lower Heights District (LSD) in Houston. Overseen by Houston-based developer Gulf Coast Commercial Group, the project aims to intertwine a curated mix of urban amenities with the quirky charm of historic Houston Heights. It would include luxury apartments, retail and office space and a hike-and-bike trail.
Home Depot would serve as an anchor tenant. The new 106,400 sq-ft metal Home Depot building would include a concrete masonry unit (CMU) perimeter wall, light metal framing on the exterior and steel columns. Due to the nature of the soils at the site, which included uncontrolled fill, Menard Group USA was contracted to provide ground improvement – the selected technique was Controlled Modulus Column (CMC)™ rigid inclusions.
Ground Conditions:
Solution:
Excavation and replacement of the deep fill was considered for the site. However, this would be impractical due to the depth of excavation and need for shoring -- and the associated construction debris, groundwater and potential for handling contaminated soils. Menard provided an economical and time-saving solution with CMCs.
The use of CMCs enabled Menard to bypass obstructions within the fill, while creating minimal spoils and minimizing the need for disposal. By virtue of the CMC design, a portion of the building footprint is supported by ground improvement (area of deep fill) and the remaining footprint is supported on grade. The General Contractor planned to “cap” the site with lime-stabilized soil (shrink/swell mitigation of plastic soils). Menard used the lime-stabilized soil as its Load Transfer Platform (LTP), in lieu of crushed aggregate, which provided cost savings for the ground improvement scope. Menard installed 453 CMCs, totaling 13,850 LF, to a maximum depth of 35 ft. Menard designed a layout of CMCs at each footing to support column loads from 25 to 100 kips. The slab on grade was designed for uniform loading of 450 psf. The design provided for 1 in of post-construction settlement with a differential settlement of less than a 1/2 in, meeting the performance criteria of the building.
For a new Home Depot in Houston, Menard successfully installed CMCs, eliminating excavation and disposal of contaminated soils.
Print this resource